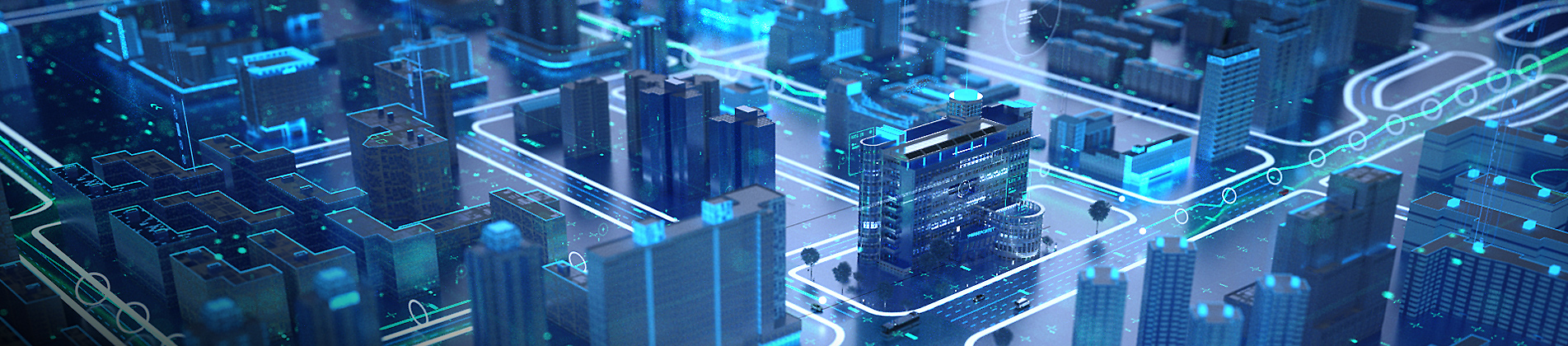
Technology
From an industry perspective, the past decade has been a whirlwind of innovation in automotive light detection and ranging (LiDAR). Numerous laser technologies and system solutions have been fiercely competing for market share. However, recent trends suggest a growing convergence on vertical-cavity surface-emitting laser (VCSEL) and antireflective VCSEL (AR-VCSEL) based solutions. This commentary, rooted in the practical realities of the industry, examines the historical trajectory of industrial laser technology for commercial automotive LiDAR. It specifically focuses on the recent applications of VCSEL/AR-VCSEL technologies and their future prospects.
An introduction to LiDAR
LiDAR (Light Detection and Ranging) was invented in the 1960s by Hughes shortly after Theodore Maiman and his team demonstrated the first ruby laser. It was initially applied in meteorology, ocean sensing, and topographic mapping. In 1971, NASA integrated a LiDAR, known as lunar Laser Ranging RetroReflector (LRRR) in Apollo 15 to map the moon’s surface, and later extended its use in the spacecraft bound for Mars and Mercury. It was not until the 2010s that LiDAR started to be applied in commercial automobiles. In the 2020s, the automotive LiDAR has become popular in high-end electric cars. Offering real-time point-cloud images enriched with object depth and velocity data, LiDAR serves as a pivotal component for both assisted driving and self-driving. There are over a hundred LiDAR companies globally. North America pioneered in commercializing automotive LiDAR with Velodyne supplying mechanical spinning LiDAR HDL-64E to numerous self-driving companies in Silicon Valley during the first half of the 2010s. This region also hosts the most LiDAR company IPOs. Asia, particularly amidst the surge in smart electric vehicle development, has witnessed a notable emergence of LiDAR companies in recent years. In contrast, Europe is marked by the dominance of traditional giants. The industry experienced some turbulence in 2022, marked by the bankruptcy filings of LiDAR pioneers Quanergy and Ibeo. However, in 2023, there was a surge in LiDAR sales driven by intense competition between Chinese EV makers. Today, key players in the global LiDAR market include Valeo in Europe, Luminar and Ouster in North America, and Hesai, RoboSense, Seyond, and Innoviz in Asia.
A typical automotive LiDAR system comprises a scanning laser, a receiver, associated optics, and integrated driver and processor circuits. It collaborates with cameras, sensors, and the position and navigation system. Functionally, automotive LiDAR falls into two main categories: primary LiDAR, responsible for long-range forward perception, and supplementary LiDAR, used for peripheral environment sensing. Together, they can achieve 360° omnidirectional perception, eliminating blind spots. The required detection range for primary LiDAR varies globally from 150 m to 350 m, influenced by several factors: diverse vehicle speed limits, the targeted level of driving automation (as classified by the Society of Automobile Engineers as six levels), and regional regulations.
Based on the detection method, LiDAR technology can be classified into two types, namely frequency modulated continuous wave (FMCW) and time of flight (ToF). FMCW utilizes the mixing of returned light with frequency-modulated transmitted light to ascertain the distance and velocity of a moving object ToF, on the other hand, determines the distance by calculating the time interval between the emitted pulse and the returned pulse. ToF is also the earliest technology used for LiDAR, e.g. in LRRR. Currently, most LiDAR manufacturers are favouring ToF technology due to its simplicity and lower cost. As a result, the following discussion will primarily focus on ToF and related laser technology.